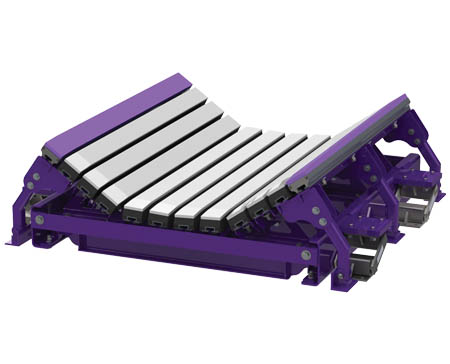
Industry
Sand and Gravel
Application
Load Zone Containment
Product
DRX™ 3000 Impact Bed
Enclosed skirting
Objective
Eliminate spillage
Reduce dust at load zone
Decrease belt carcass wear at load point
Conveyor Details
60" rubber belt conveying gravel at 750 FPM and 3500 TPH
Problem:
The maintenance team at a Texas gravel plant was looking forward to less spillage in the load zone when a new Flexco DRX™ 3000 Impact Bed and Enclosed Skirting System was ordered and installed. So, when the seal busted after only a week of use, they were perplexed. As far as they knew, everything was considered when they were specifying the containment system. So, they called in the local Flexco Territory Manager to take a look at the product and make sure it was installed correctly.
Solution:
Immediately upon his arrival, the Flexco representative noticed that transition distance and belt elevation were not considered, and the top of the pulley was higher than the idler center cans. This created a partial trough transition, which can fold the belt up faster than a full trough transition if done correctly. In this case, it was not executed properly, which caused the belt to ride out of the trough when the belt was empty. When the belt is loaded with material, this can cause the belt to drop below the sealing section, leaving a large gap between the skirt wall/sealing material and the belt. No solid seal resulted in no material containment.
Result:
To fix this, the team was instructed to simply lower the tail pulley to be the exact same height as the top of the troughing center idler can. The DRX 3000 and Enclosed Skirting System were then adjusted, and the dust and spillage problems were eliminated thanks to a solid bed and effective seal.