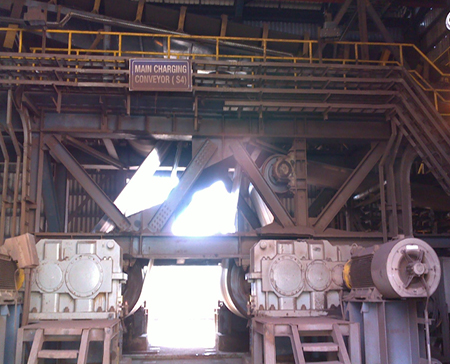
Industry
Steel Application Conveyor belting leading to blast furnace at major steel plant in India
Product
PT Max™ Belt Trainer
Objective
To eliminate the swaying of conveyor belt resulting in premature belt failure, and to provide a solution that not only increases the life of the belt, but also reduces spillage.
Conveyor Detail
Belt carries iron ore, sinter, coal, dolemite, limestone, and quartzite. Conveyor belt is 600 m long, 2000 mm wide, and the speed is 2.2 m/s.
Problem
The largest integrated private steel manufacturer in India in terms of installed capacity had a problem with belts mistracking, causing spillage and belt damage. The main concern was with the BFC3 belt carrying iron ore, sinter, coal, dolomite, limestone and quartzite from bins to the blast furnace. The plant’s manager requested a solution that not only increases the life of the belt but also reduces the spillage.
Solution:
After close inspection, the decision to install belt trackers was made. The plant manager ordered six PT Max 84” Return and four PT Max 84” Top Side units.
Result:
After installation was complete, a trial run was executed and found a local belt tracker was hindering the performance of the PT Max. After adjusting the belt tracking, the senior manager at the blast furnace at the plant noticed the belt was running in the centre and was pleased with the results. Understanding the maintenance requirements of the system, they now check the return idlers, pivot and tilt action of the frame, guide idlers, and ensure that the sway is under control each month. The customer is happy with the overall performance of the product and feels that they have found the right fit for the future of the plant.